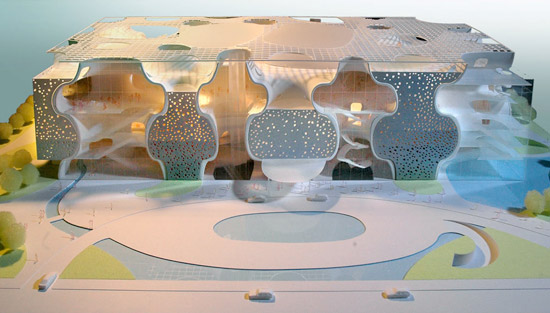
construction begins of the taichung metropolitan opera house, designed by toyo ito.
the ground-breaking ceremony for the second-stage main construction of the taichung
metropolitan opera house was held on dec. 3, 2009.
the theater is expected to cost NT.36 billion (US5 million) and will take over four
years to complete. the opera house is now on track for a december 2013 ribbon-cutting.
according to taichung city officials, the project was put up for bid five times over the past
several years but failed to attract suitable tenders due to associated engineering challenges.
while other major cities in taiwan are all known for something, taichung, a city of roughly
1 million residents whose name means 'central taiwan' in chinese, has trouble finding
anything to distinguish itself from taiwan's other metropolises. today it is seen as one of
the most cultural cities in taiwan.
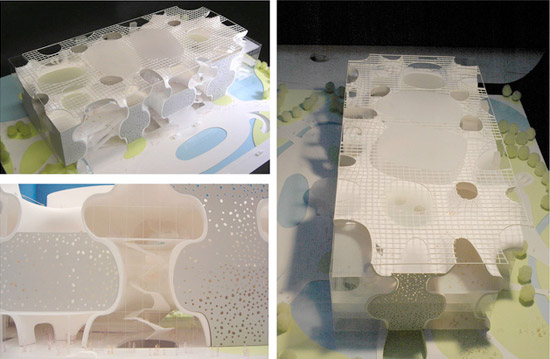
model of the taichung metropolitan opera house
the main structure will be formed with several connecting curved walls, inlaid floors,
inlaid interior and exterior walls, and a core service wall. the curved wall structure will
be formed with 58 curved wall units, creating many complications in building steel bar
reinforcements and steel trusses. the construction technique is the first of its kind in the
world of architecture and has never been seen before in the taiwanese engineering industry,
which meant that many local construction companies failed to show interest in participating
in the project. in order to acquire the cooperation of the ideal company, the city government
visited many potential collaborators and finally signed a contract with lee ming construction.
wu chun-shan, president of lee ming construction, said building such a structure containing
three-dimensional curved walls was generally thought impossible.
'but we are making the impossible possible'.
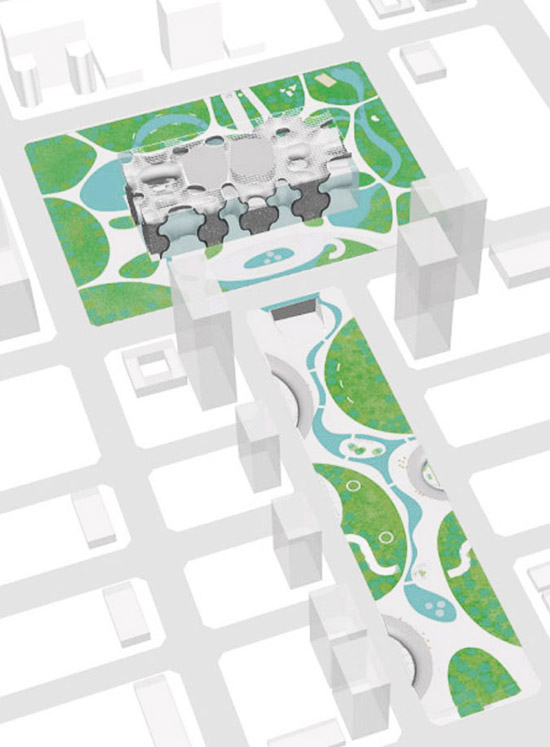
drawing of the taichung metropolitan opera house
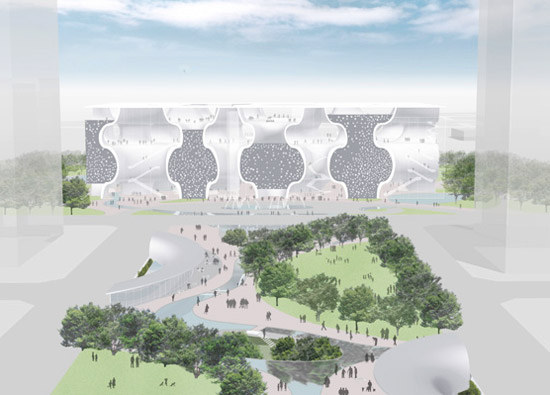
drawing of the taichung metropolitan opera house
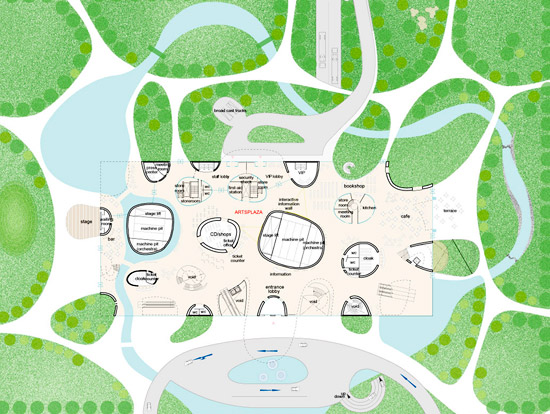
integrated in the landscape
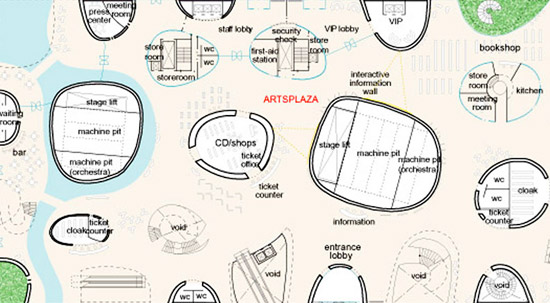
spatial organization
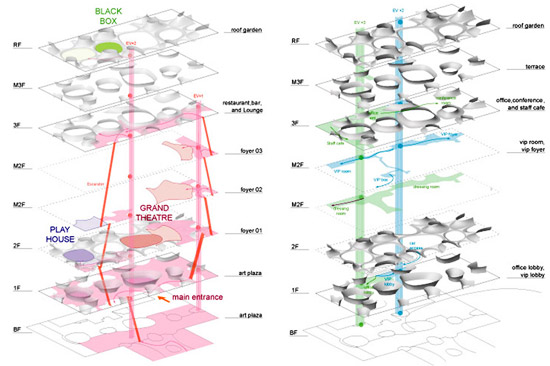
left: audience circulation, right: VIP and office circulation
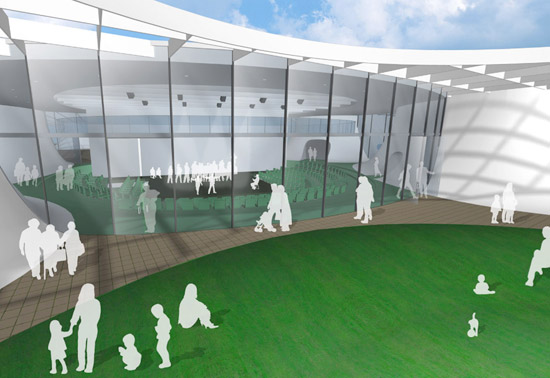
ito’s work has been highly concerned with the notions of an all-encompassing, ever expanding space.
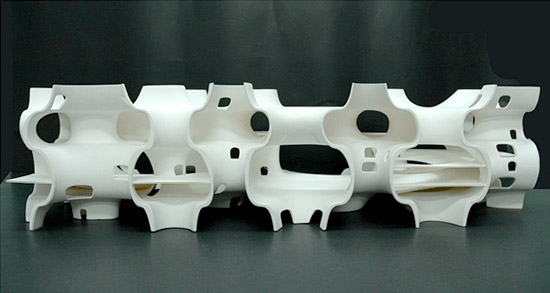
a nearly 4m large-scale model. ito made full-scale structural models to simply prove its integrity.
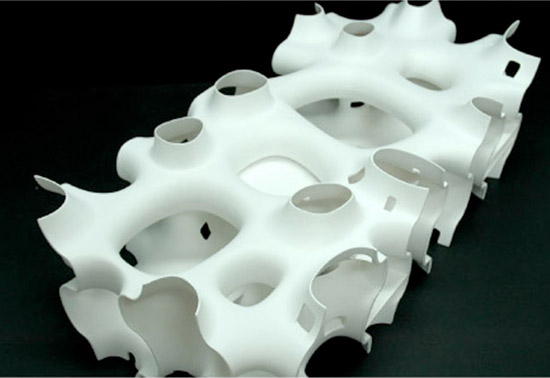
continuos surfaces in an open structure which actively engages its surroundings in all directions
and creates great opportunities for artists and visitors, stage and auditorium, interior and exterior.
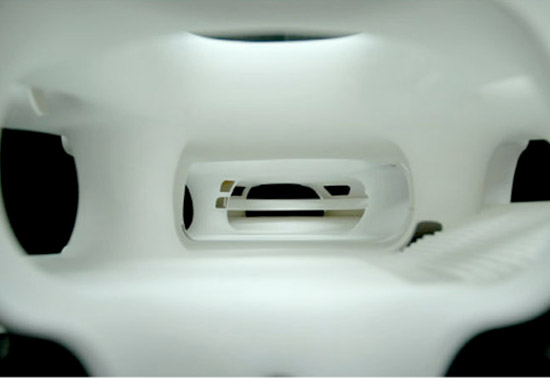
toyo ito calls this space the 'sound cave', a horizontally and vertically continuous network.
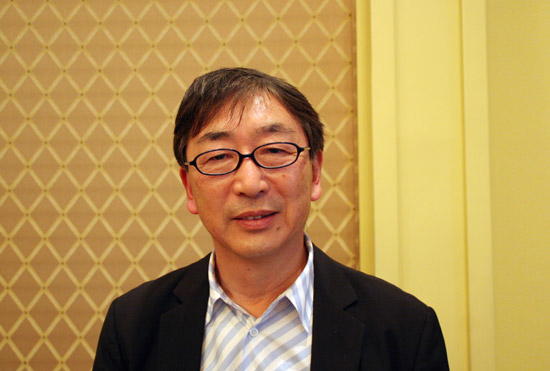
toyo ito
portrait © designboom
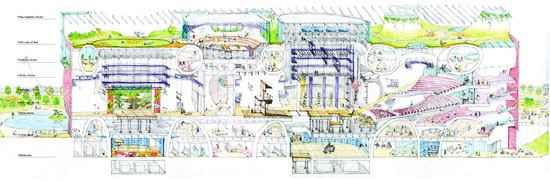
illustration by studio toyo ito
issues of the environment, resources, and energy
1. recycling of rainwater and sewagethe rain falling on the large roof surface will be collected and filtered for use in
irrigation and sprinkling for landscaping plants, etc. sewage from the facility will be
processed in a purification tank to approximately 5ppm BOD and 5ppm SS, and then
reused as an intermediate water supply for purposes such as toilet flushing.
2. use of eco-materials
the majority of materials used will be recyclable eco-materials. this helps to limit the
environmental load and conserve resources, thereby contributing to the reduction of
carbon dioxide emissions and prevention of global warming.
3. adjusting the surrounding environment for energy savings
when adjusting the environment of an architectural space, it is not enough to devote
one's energies solely to the load inside the building. it is also essential to arrange the
environment outside the building in a way that reduces the load inside the building.
in this plan, we have given consideration to increasing greenery, creating shade, and
using the evaporative latent heat of water.
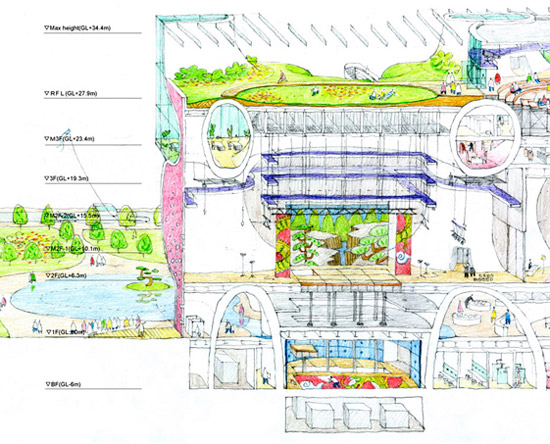
part 1
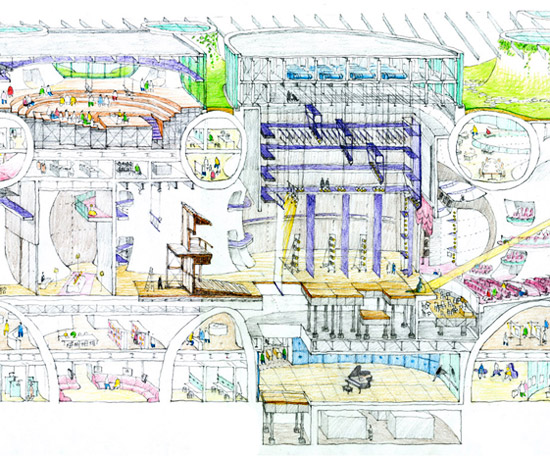
part 2
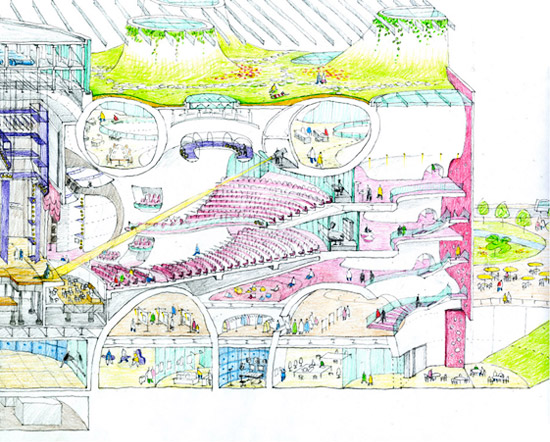
part 3
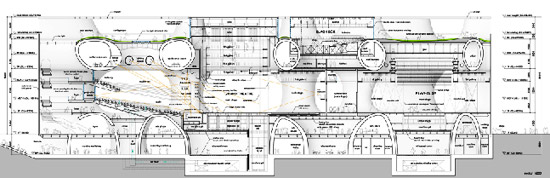
section drawing
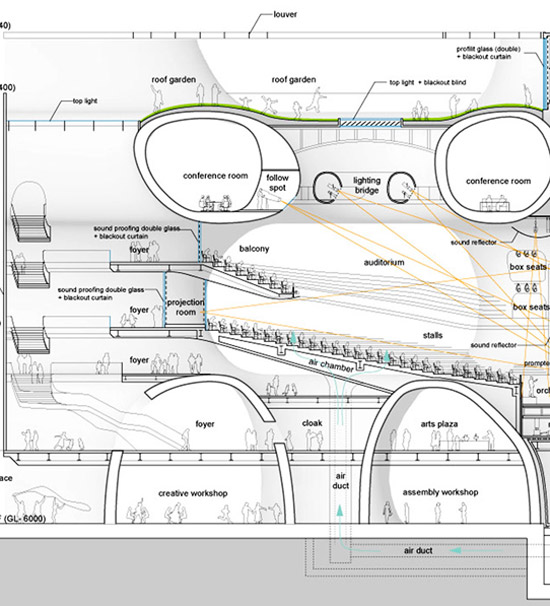
part 1
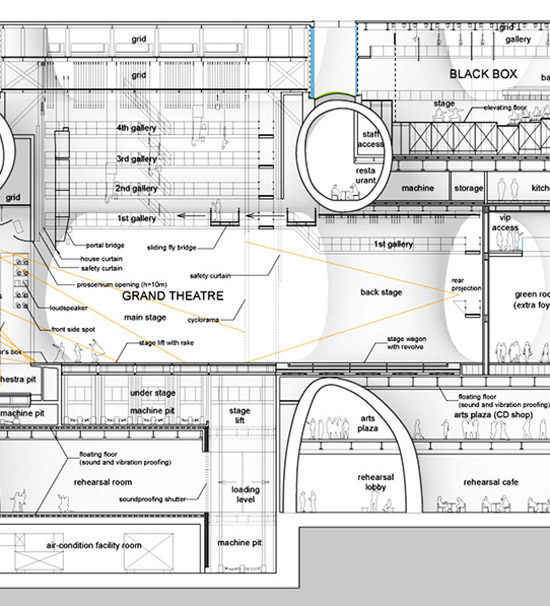
part 2
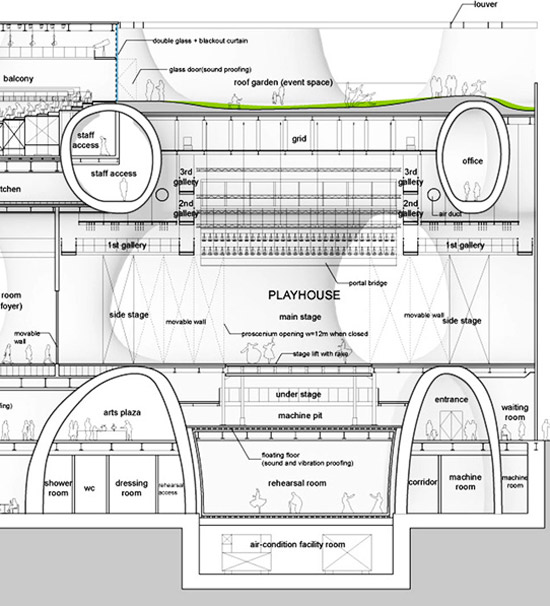
part 3
construction process
the structural system is developed together with the constructionmethod to realize the freeform geometry in rational and efficient manner.
the freeform concrete surfaces are shotcrete (spray concrete). it is commonly
utilized for tunnel construction and suitable for curved surface. it can be shot
horizontally or vertically. rather than constructing doubly curved formwork that is
expensive and time consuming on site, the temporary structure in the void creates
faceted surfaces that best-fit the finished surface. between the temporary steel work,
expanded metal mesh is expanded metal mesh spans between the temporary steel
work to act as faceted formwork. 150 mm thick concrete can be shot at one time.
the surface layer of 25 mm is shot separately without large aggregate to achieve
smooth surface finish. concrete thickness varies between 200 mm at the top floor
and 350 mm at the bottom.
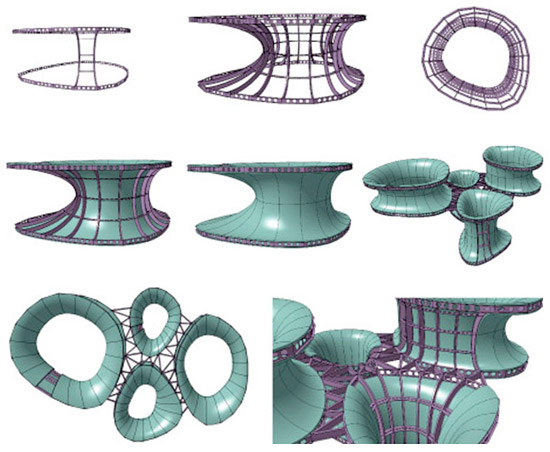
challenging technique
sprayed concrete construction method
typically, an expanded metal mesh is used as a permanent back shutter to which the
the reinforcing mesh is affixed. the concrete is sprayed onto the expanded metal
and the reinforcement is fully enclosed. the concrete is typically sprayed using one of two
methods. with the dry process, the dry constituents of the concrete are mixed in a portable
batching plant and the water is added to the mix at the nozzle. with the wet process, the
water is added to the batching plant and premixed with the dry constituents and the wet concrete
is sprayed from the nozzle. the benefits of the wet process are that there is greater control over
the concrete mix as the concrete is often mixed off site by ready-mix contractors and delivered in lorries.
it is common practice to apply the concrete in two layers. the first thick layer is usually applied using
the wet process. once sufficiently cured, a second, thin finishing layer is then applied using the dry process.
the reinforcing mesh is affixed. the concrete is sprayed onto the expanded metal
and the reinforcement is fully enclosed. the concrete is typically sprayed using one of two
methods. with the dry process, the dry constituents of the concrete are mixed in a portable
batching plant and the water is added to the mix at the nozzle. with the wet process, the
water is added to the batching plant and premixed with the dry constituents and the wet concrete
is sprayed from the nozzle. the benefits of the wet process are that there is greater control over
the concrete mix as the concrete is often mixed off site by ready-mix contractors and delivered in lorries.
it is common practice to apply the concrete in two layers. the first thick layer is usually applied using
the wet process. once sufficiently cured, a second, thin finishing layer is then applied using the dry process.
it is essential that the finished product is cured appropriately to mitigate shrinkage and to ensure that
design strength is achieved. spraying concrete is a messy process. some concrete will rebound and
some will pass through the expanded metal back shutter. it may be necessary to install temporary
protection to avoid polluting the surrounding area.
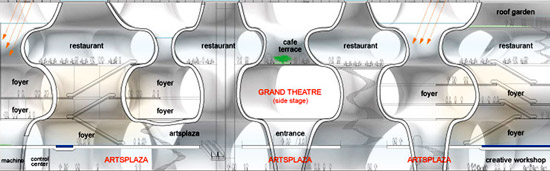
grand theatre
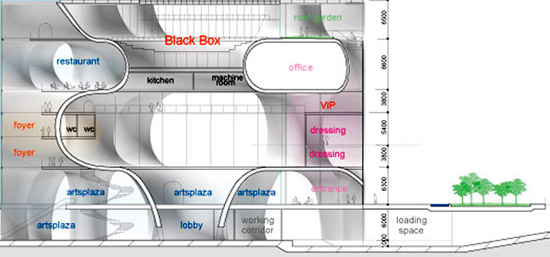
black box
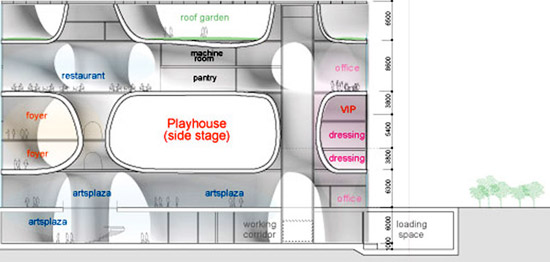
play house
site area: 57,685 square meters
floor area: 43,264 square meters
2009 seat grand theatre 4,450 m2
800 seat playhouse 1,770 m2
200 seat black box 520 m2
backstage space 2,630 m2
other space 16,090 m2
management space 1,850 m2
arts plaza 6,000 m2
arts/creative workshop 3,100 m2
total 36,410 m2
design strength is achieved. spraying concrete is a messy process. some concrete will rebound and
some will pass through the expanded metal back shutter. it may be necessary to install temporary
protection to avoid polluting the surrounding area.
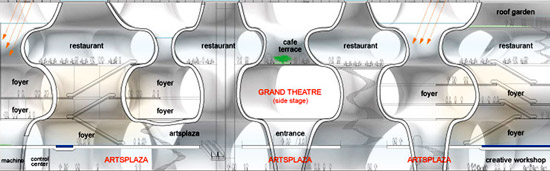
grand theatre
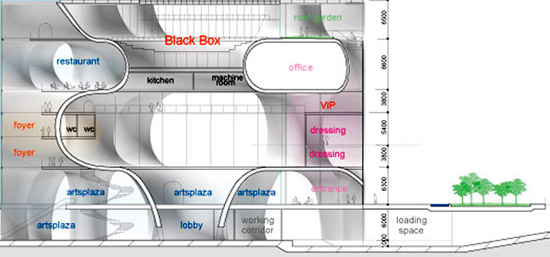
black box
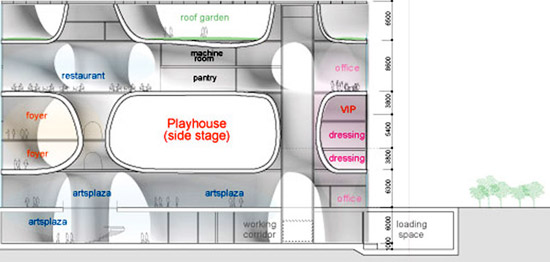
play house
site area: 57,685 square meters
floor area: 43,264 square meters
2009 seat grand theatre 4,450 m2
800 seat playhouse 1,770 m2
200 seat black box 520 m2
backstage space 2,630 m2
other space 16,090 m2
management space 1,850 m2
arts plaza 6,000 m2
arts/creative workshop 3,100 m2
total 36,410 m2